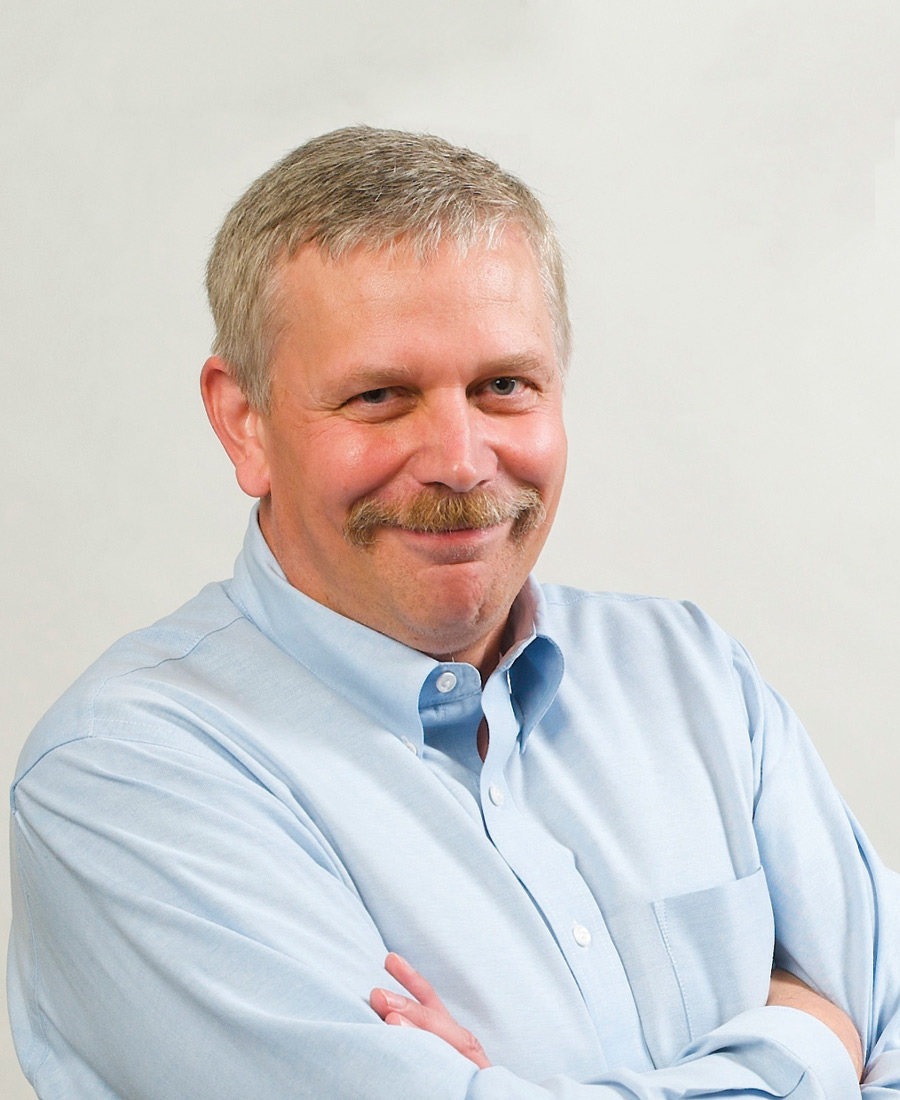
The Engagement Effect
Report
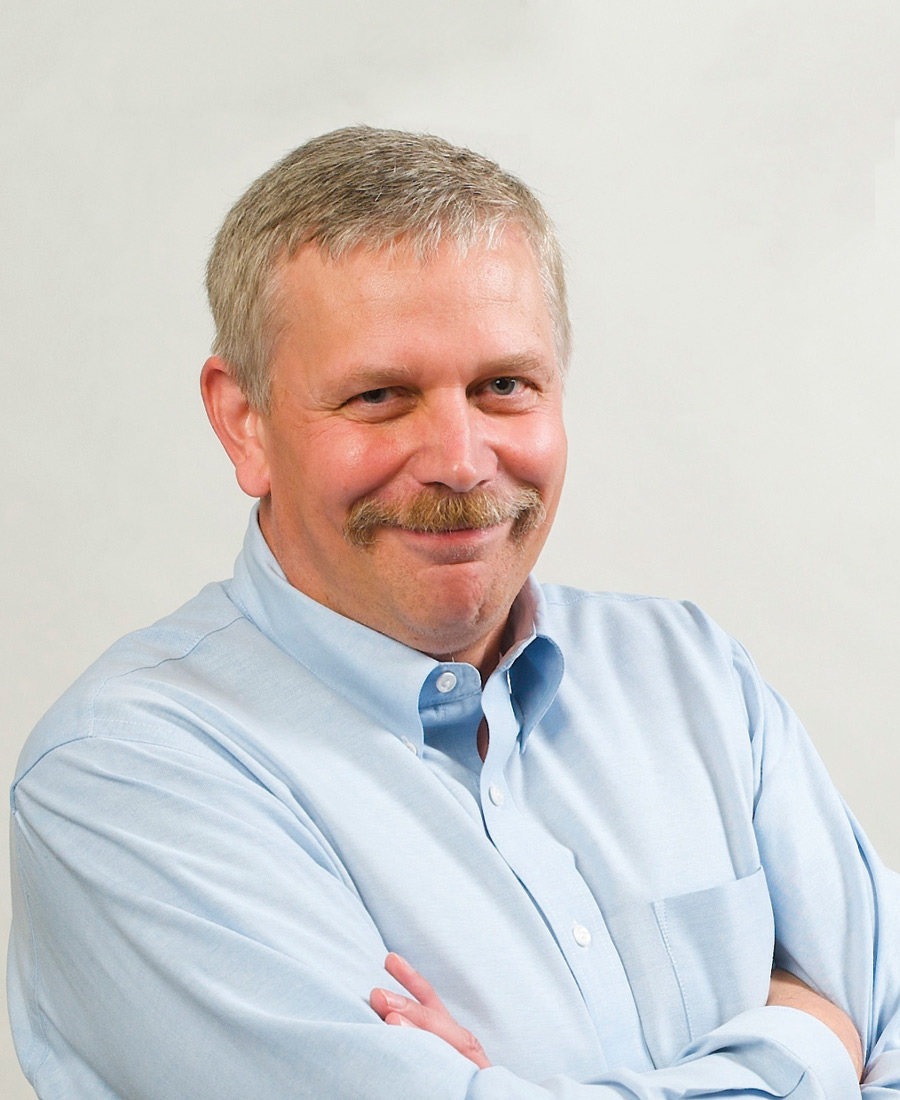
The Engagement Effect
Report
ccording to the US Bureau of Labor Statistics, in 2002, the overall accident rate for the construction industry in Alaska exceeded the national average. This accident rate was deemed unacceptably high by the Alaska Department of Labor, Alaska Occupational Safety and Health, or AKOSH. The Construction Health and Safety Excellence Program, or CHASE, was developed to address this issue.
I sat in on a recent presentation on the CHASE program, delivered to the local chapter of the American Society of Safety Professionals and then had the opportunity to interview Donald “Donnie” Farwell, the CHASE program director for AKOSH, about the current CHASE program in Alaska.
Ross: What is CHASE all about?
Farwell: CHASE is a partnership between construction companies and the state of Alaska. At the base level, the program is designed to assist companies in improving their safety culture. At a higher level, it is designed to help companies that may not be proficient in safety build a foundation that can be built upon. My hope is that as we continue to grow this program, contractors will become more familiar with our programs and not look at us as just an enforcement agency, but understand the support that we can add through consultation.
Ross: CHASE has been around a long time. I wrote an article for Alaska Contractor about CHASE over ten years ago; what is new now?
Farwell: As you saw in the presentation, we had a time where all but two companies were removed. Twelve companies were part of the CHASE program prior to 2018. Ten were removed due to a lack of commitment by both the contractor and AKOSH. This was an issue that involved both the AKOSH and the contractors and centered around communication. The good news is that communication issue has been resolved. We are using an updated Standard Operating Procedure (labor.alaska.gov/lss/AKCHASE/SOP_005_CHASE_Final.pdf) to ensure there is not a repeat. This includes mandatory quarterly contact, annual data submission, and a CHASE report that we produce here and distribute.
Ross: I see there is a lot of useful information in that guidance document. This will answer a lot of questions for potential applicants about the process. What are the benefits of being CHASE certified for a contractor?
Farwell: Being in CHASE gives quite a few incentives. In my opinion, the top two are programmed inspection exemptions and the penalty reduction in the event a contractor does receive a citation. However, for the smaller companies, the ability for us to work closely with them and conduct hazard recognition evaluations and on-site training for their employees may be a bigger benefit. I have seen a change in the mindset of open communication, especially in our subcontractor partners. They are very vocal with their general contractors when it comes to hazards on a job site.
Ross: The programmed inspection exemptions are great, but it sounds like a better benefit for participants are the opportunities to grow and improve their safety programs. There are some very interesting data regarding that on the website and in the guidance document. What are the benefits for AKOSH?
Farwell: For us, I think it is multi-faceted. First and foremost, construction is an inherently dangerous job regardless of the level you are working at. Since construction sites generally have multiple contractors on them at a time, we get to reach out to a variety of different trades. In turn, the information, training, and experience that we have with them gets passed on to their next jobsite. Secondly, anytime you hear OSHA on a jobsite, people tend to scatter or shut down. Working with our partners has opened the doors to several other contractors that may have not understood what the consultation program can do or that there is more to OSHA than just shutting down projects and fining companies.
Ross: You mention partnership, what does that mean?
Farwell: As the definition alludes to, working together for a common goal. In our case, the continual improvement of safety practices within the construction industry. I think of it as a dual learning program. I have done construction (for the Navy) for over twenty years and have a solid background; however, I learn something new from every company that I work with. Likewise, I have seen some of the best safety practices around the world and been able to add insight to quite a few programs with our partners. For those really stubborn or odd tasks, working as a team with multiple partners and varying years of experience allows us to tackle some really complex tasks.
Ross: How hard is it to achieve? Is it only for large contractors or can a smaller contractor do it?
Farwell: We prefer smaller contractors since they typically have less staff to dedicate to safety and tend to overlook some items such as written programs. However, contractor size really doesn’t matter. The most difficult aspects from my perspective are the commitment to work with us and, if a contractor does not meet the minimal requirements, getting them to build a good foundation for safety that we can assist with developing. Companies are still hesitant to have AKOSH openly invited to their project sites, though we are working on that perspective.
As long as your NAICS code is 23XXXX, you are welcome to apply. For general industry, there are programs such as Voluntary Protection Program (VPP) and Safety and Health Achievement Recognition Program (SHARP). SHARP does not have a good fit for construction since it is more site-specific and many construction contractors do not have the depth both in safety or administration to apply for VPP.
Ross: I see there is a pretty extensive application process that also involves site visits. After completing the application, a comprehensive consultation visit will include a review of the employer’s safety and health management program. How long does it take to get certified?
Farwell: The length of the process can vary depending on a variety of factors. The biggest delays that I have seen are typically centered around programs and implementation of those programs. Many times, I see a company that has a fantastic safety plan that is well developed and thorough; however, it simply collects dust or there are no programs at all. On average, I have a six-month turnaround from start (application) to approval (from the Commissioner). COVID slightly complicated this process since we didn’t want to expose our contractors unnecessarily and cause a shutdown of a jobsite. Additionally, we require three consultation visits at a minimum for program entry. Depending on the work in progress from a company, it can be difficult to identify three different jobsites to visit.
Ross: I understand there are three levels of CHASE: what does each level mean and how do you qualify?
Farwell: Each level gets progressively more thorough. The Blue level is pretty basic, similar to the OSHA standards. If you are following the standards and willing to commit, it’s fairly easy to get into. The Gold level involves a little extra administrative work and relates mostly to supervisor positions. For example, this level requires the attainment of OTI 500 or similar course, a substance abuse program, supervisor level training for all supervisors, and effective employee involvement. The Flag level is the most complex and almost at a level similar to the VPP. Supervisor-type training is required at all levels of employees within the company. The company must show employee involvement in all aspects of the safety program, and for general contractors they must ensure all site-specific safety plans are used by all subcontractors and that those plans are equivalent to or superior to their own programs. Finally, they must not have received any willful or repeat violations in the past three years and have no catastrophe or fatalities in the same timeframe. The complexity of this level will eliminate many of the subcontractors (though not all).
More information about the CHASE program is available at labor.alaska.gov/lss/ak_chase.htm
Farwell: There are currently six companies active. Three are CHASE Gold: Cornerstone Construction, Watterson Construction, Dawson Construction. Three are at CHASE Blue level: Vannoy Electric, Alaska Specialized Constructors, and H5 Construction. There are no current Flag participants.
Ross: I see there are annual requirements such as submitting incident investigations and training provided for the previous year; OSHA 300 log; list of hazards identified and abated; Workers’ Compensation injury information (summary) and visits. Is it difficult to maintain CHASE status?
Farwell: Maintaining CHASE in the past was an issue, especially with our turnover rate. However, we have made it much more transparent and included a few layers of requirements on our part before a company is removed from the program. The essence of maintaining CHASE status is the yearly submittal. A company must submit the required documentation by March 1 of each year. This data is recorded, analyzed, and compared to previous years (depending on how long the company has been in the program). An executive summary is developed based on the information they submit and the visits that we conduct during the calendar year. If they are meeting the requirements for their particular level within the program, I recommend approval to keep their status. If they are not meeting the requirements, I recommend removal and provide that to the Chief of Consultation for a final decision.
Ross: What is coming next for CHASE?
Farwell: The future plan for CHASE is to rebuild the program. We took a hard hit when most of the companies were removed and are working with some of the previous members to get them back in. Rebuilding trust can be difficult, but when I first volunteered to take this program on (approximately three years ago), I committed to bring the program back only when I felt it was solid and sustainable. I didn’t want a repeat of what happened before I checked in. I have a little more work to do, but am making really good progress. The final step for me is to get a few more companies into the program and validate the value of what can be accomplished. I would expect by next year that I will be able to do that.