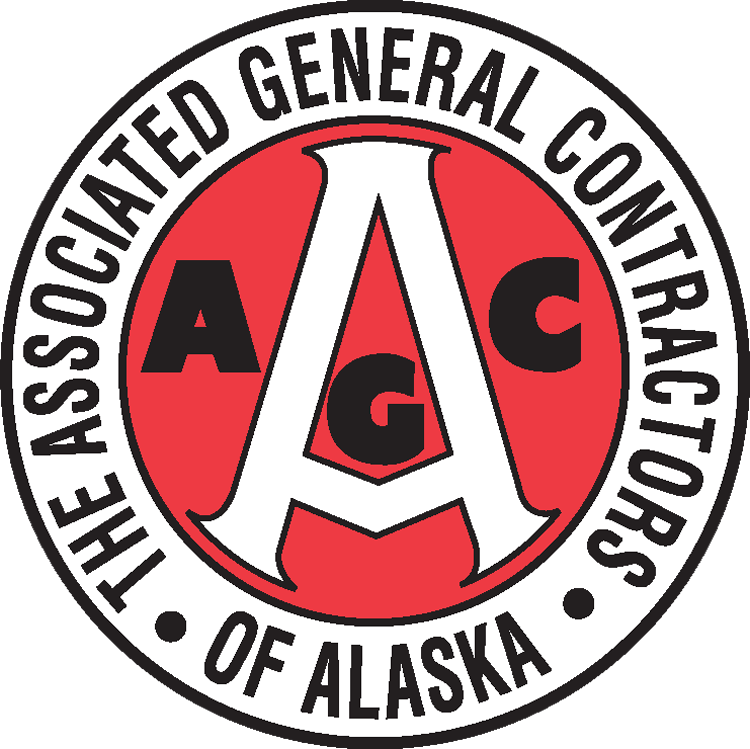
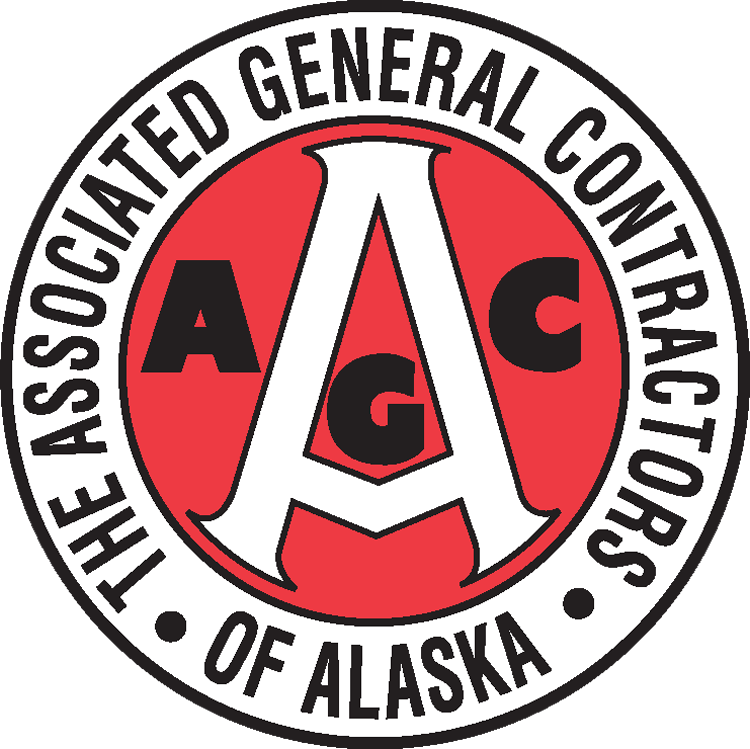

ith a slogan like, “The best way to get our attention is to say, ‘That can’t be done!’” you know a company is going to be special.
Lifewater Engineering Company Operations Manager Jerry Fleishman says his company is the only one of its kind in the state that manufactures arctic-engineered, onsite wastewater treatment systems.
“We’re also the largest plastic fabricator in the state,” he says.
From engineering and design to manufacturing, installation, and product operation, the company does it all.
Fleishman says Bob Tsigonis, Lifewater founder, took the question to God, an answer came to go ahead, and Lifewater moved from strictly engineering to design and manufacturing.
It has been growing steadily since. In 2005, Lifewater started designing and fabricating above-ground wastewater treatment systems out of welded thermoplastic sheets in their Fairbanks plant for a variety of clients, including the R.G. White Large Animal Research Station at the University of Alaska Fairbanks, Alyeska Pipeline Service Company, and ExxonMobil. The wastewater treatment systems gained a reputation of being solid, long lasting, and simple to maintain.
“Close to 400 units of various sizes, in different communities across the state, have been installed, including our original STP [sewage treatment plant] from 1998 that is still running,” Fleishman says.
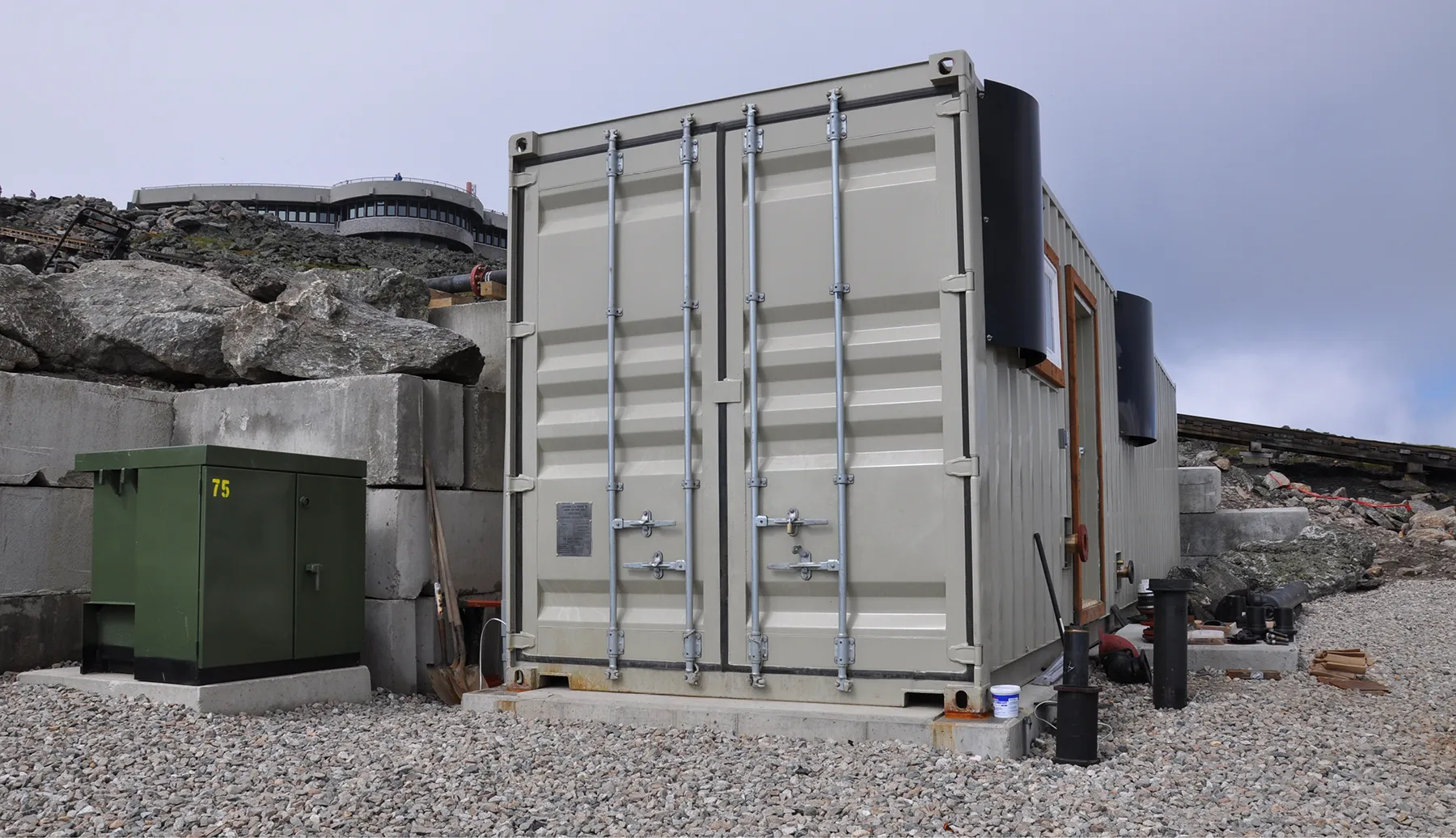
What could have been a wrench in the works for another company might turn out to be a catalyst for the right solution for Lifewater.
“It’s my perspective that people wait too long before seeking a solution,” he says. “It’s the, ‘I need this right now!’ call for help that Lifewater responds to so well.”
He says Lifewater prides itself on being flexible and nimble.
On one project they had ninety days to design, procure, permit, build, and then ship out a treatment system on a Lockheed C-130 Hercules, a four-engine turbo-prop airplane with a 42,000-pound payload. The project involved creating a 2,500-gallon-per-day drinking water treatment system and a 2,500-gallon-per-day wastewater treatment plant.
“That was a fun challenge,” he says.
A small, energy-efficient fan keeps odors and moisture out of the structure.
Made of impact-resistant, high-gloss, recyclable polypropylene, the solids are separated from the liquids to mitigate smell and speed up the drying process. The dried solids can be burned, composted onsite, or dumped into the outhouse. There are multiple options for the urine: disposal in a small graywater leach field, disposal in an outhouse, or utilized as a fertilizer.
Both are a practical solution to every rural and Bush Alaskan’s long-held dream to never use a honey bucket again.
Jerry Fleishman, Lifewater Engineering Company
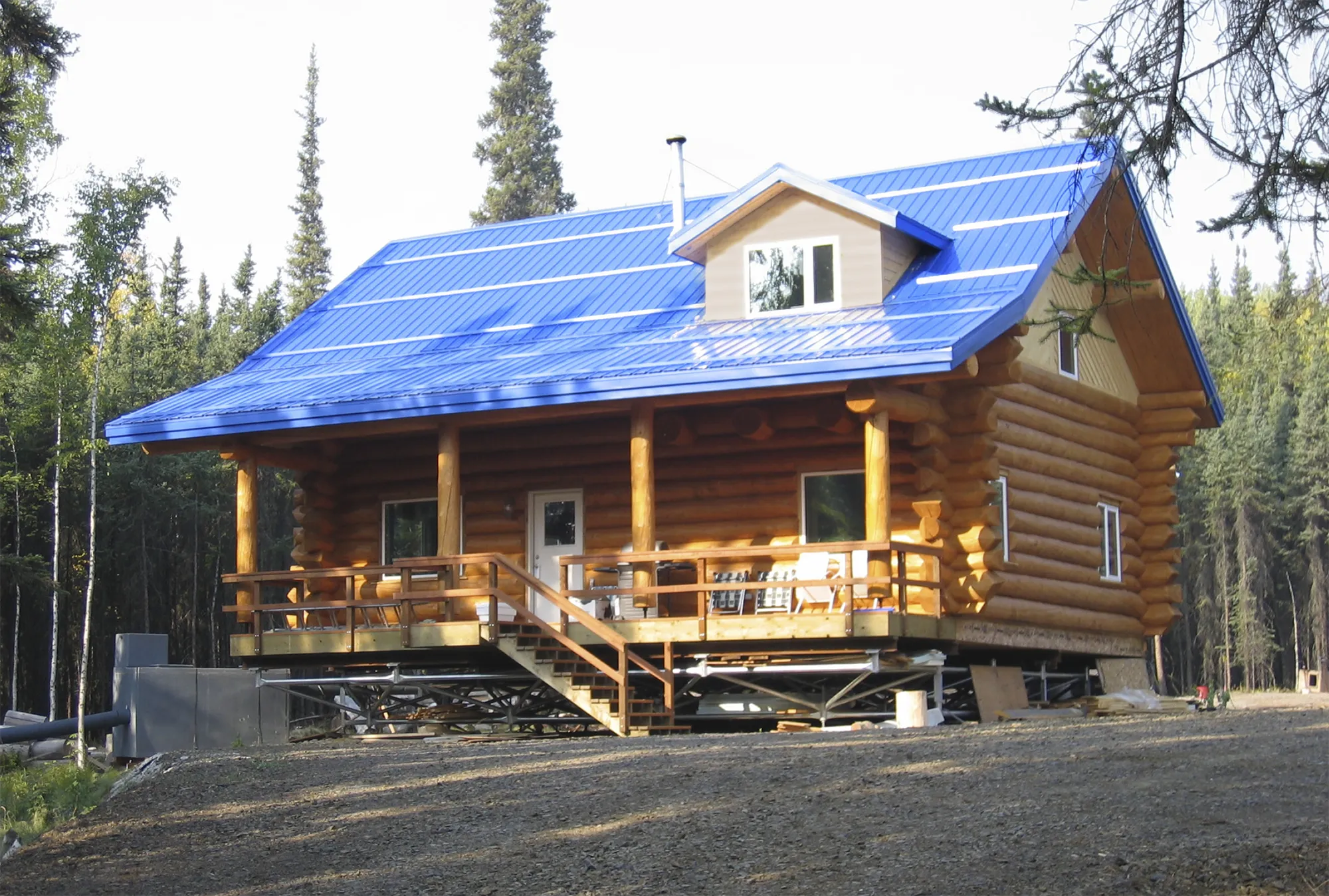
“We noticed that not a single one of our tanks had a failure in the structure; the plastic we use naturally floats; and this material does not break down under UV. It is also a Rough Duty material that can withstand extreme temperatures. It is the perfect material for our Rough Duty Boat, the toughest boat on the water,” says Fleishman.
The question they asked themselves was: “If plastic is good enough to put on the bottom of the boat, why not build the whole boat out of it?”
“This was uncharted territory for us,” says Fleishman.
They asked God for wisdom through prayer as they began this journey of boat manufacturing.
Based out of Fairbanks, Lifewater’s location allows access to a variety of nearby rivers, and the shop is located adjacent to a float pond, providing testing grounds out the plant’s back door.
“We have even been known to plow out a boat ramp in March to get to open water,” Fleishman says.
The company makes boats for commercial use, as well as for pleasure-boating: jet boats, dinghies, and skiffs.
“We focused on product development for nine years and saw very early on that plastic was a durable, long-life, and high impact material to use,” Fleishman says.
Only virgin plastic is used.
“Though the plastic itself can be recycled, we don’t use recycled plastic,” he says. “With recycled plastic there can be quality issues, and it may cause structural integrity issues. This factors in when you’re 100 miles from nowhere.”
The company plans to expand into the design and construction of ocean-going vessels in the near future.
“We are a very specialized contractor, but we have an amazing team of mechanical, civil, and environmental engineers, as well as a shop full of great fabricators,” Fleishman says. “Right now we are looking forward to the summer’s larger commercial projects.”