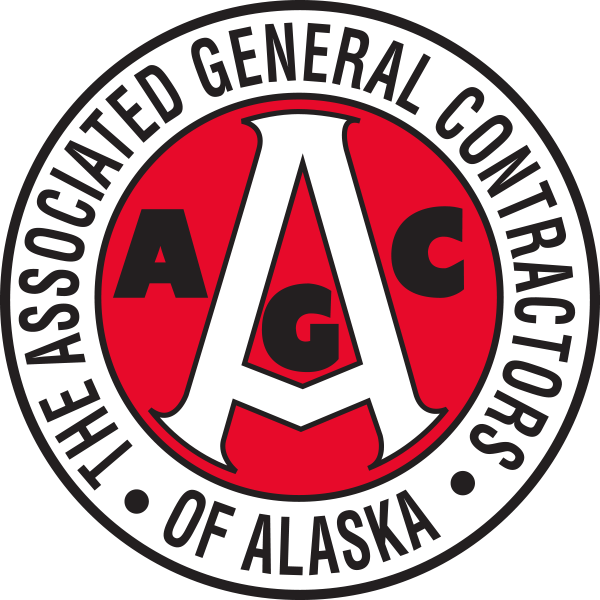
Update
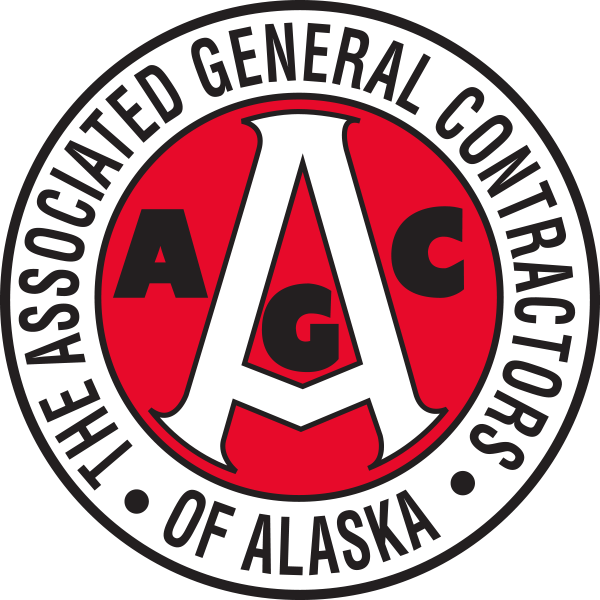
Update
ood planning and preparation are the keys to success in any construction project, but getting ready for remote work on Shemya Island takes project management to the next level.
“Shemya is a harsh marine environment at the edge of the Aleutian Islands,” says Jacob Pomeranz of Electric Power Systems. “It’s out there.”
Shemya Island is a logistically challenging location, located about 500 miles from mainland Russia and about 1,500 miles southwest of Anchorage, at the western edge of the Aleutian Chain. It’s so far to the west that it observes the Hawaii-Aleutian time zone, which is an hour behind mainland Alaska.
Getting to the island requires military clearance and a chartered flight, as it is home to Eareckson Air Station—formerly known as Shemya Air Force Base—and the Cobra Dane Phased Array Radar Facility, which is currently operated by the US Space Force and has been used to monitor space and missile activities. The radar has been in operation since 1977.
For the past decade, Electric Power Systems, or EPS, has been working on Shemya Island. Most recently, EPS and two of its sister companies—Electric Power Constructors and Mechanical Builders, Inc.—subcontracted under Brice Environmental to complete a two-year project that upgraded Cobra Dane’s existing electrical and mechanical infrastructure with state-of-the-art technology.
ood planning and preparation are the keys to success in any construction project, but getting ready for remote work on Shemya Island takes project management to the next level.
“Shemya is a harsh marine environment at the edge of the Aleutian Islands,” says Jacob Pomeranz of Electric Power Systems. “It’s out there.”
Shemya Island is a logistically challenging location, located about 500 miles from mainland Russia and about 1,500 miles southwest of Anchorage, at the western edge of the Aleutian Chain. It’s so far to the west that it observes the Hawaii-Aleutian time zone, which is an hour behind mainland Alaska.
Getting to the island requires military clearance and a chartered flight, as it is home to Eareckson Air Station—formerly known as Shemya Air Force Base—and the Cobra Dane Phased Array Radar Facility, which is currently operated by the US Space Force and has been used to monitor space and missile activities. The radar has been in operation since 1977.
For the past decade, Electric Power Systems, or EPS, has been working on Shemya Island. Most recently, EPS and two of its sister companies—Electric Power Constructors and Mechanical Builders, Inc.—subcontracted under Brice Environmental to complete a two-year project that upgraded Cobra Dane’s existing electrical and mechanical infrastructure with state-of-the-art technology.
In an August 2022 fact sheet, the US Missile Defense Agency, or MDA, describes the Cobra Dane radar as part of the nation’s Missile Defense System. It is huge: the radar face is about 95 feet in diameter and the overall radar height is 120 feet. It can detect objects up to 2,000 miles away. The recent upgrade, according to MDA, improved its coverage by “providing acquisition, tracking, object classification, and data that can be used for cueing, launch of interceptor missiles, and course updates of interceptors while retaining the site’s legacy intelligence and space track missions.”
EPS started planning for the project in November of 2020 and began design work eight months later in June of 2021. It started at just 35 percent design, accounting for the logistics of getting long-lead materials approved by the government and shipped to the island in time for the 2022 summer construction season.
“The logistics, planning, and project construction planning really started before we had 100 percent design of major equipment,” says Pomeranz. “That was one of the biggest hurdles we had to overcome. Not only did we have to get materials to site, but we also had to get vendors to guarantee that they could beat the barge to get it out there.”
Facing logistical challenges for completing work on Shemya Island is nothing new for EPS. Many of its employees have completed smaller projects on the island.
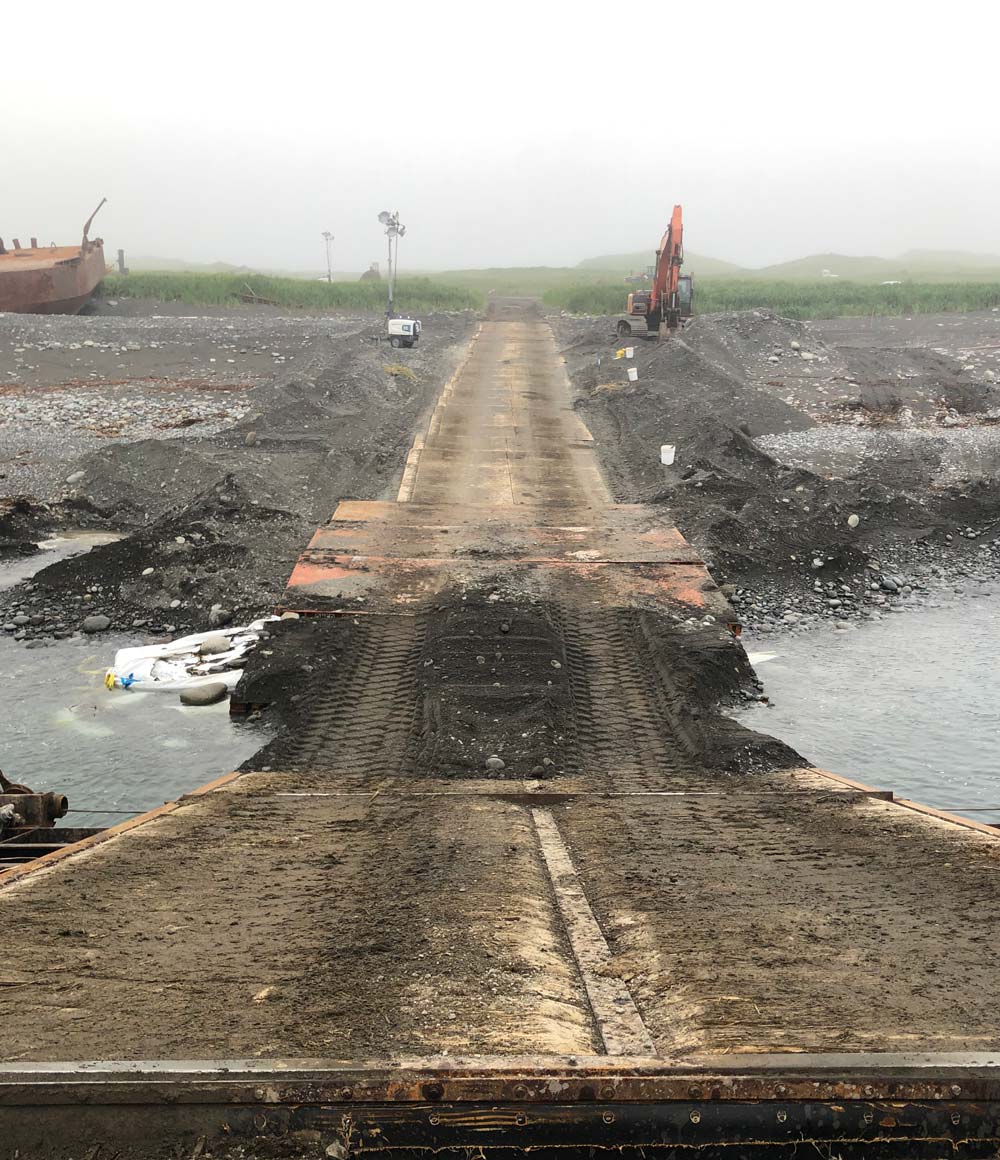
Photo courtesy of Eric Sumpter
“We’re lucky to have retention,” says Pomeranz. “It has definitely helped us work on Shemya.”
The window for Shemya Island barge traffic starts around the middle of April and ends in early to mid-September, says Eric Sumpter, a project manager for Brice Environmental.
To get materials to the island, Brice relies on two logistic legs. First, it coordinates with other shipping companies that perform normal runs between Seattle and Anchorage. From Anchorage, Brice uses truck or rail to get materials to Seward. From Seward, the materials are loaded onto a beach landing craft that is owned by Brice Marine. Once the beach landing craft reaches Shemya Island, the boat noses its way onto a sandy beach. Materials are unloaded and a temporary road is built on the sand so that materials can reach their destination.
Brice uses the beach landing craft for several reasons, but the main one is that Shemya Island’s fuel pier suffered heavy damage from a storm in February 2020. The outer sheet pile layer failed and separated from the pier.
“The only barges that are able to get into Shemya are the fuel barges,” says Sumpter, “so it gives us a huge advantage to have those beach landing capabilities.”
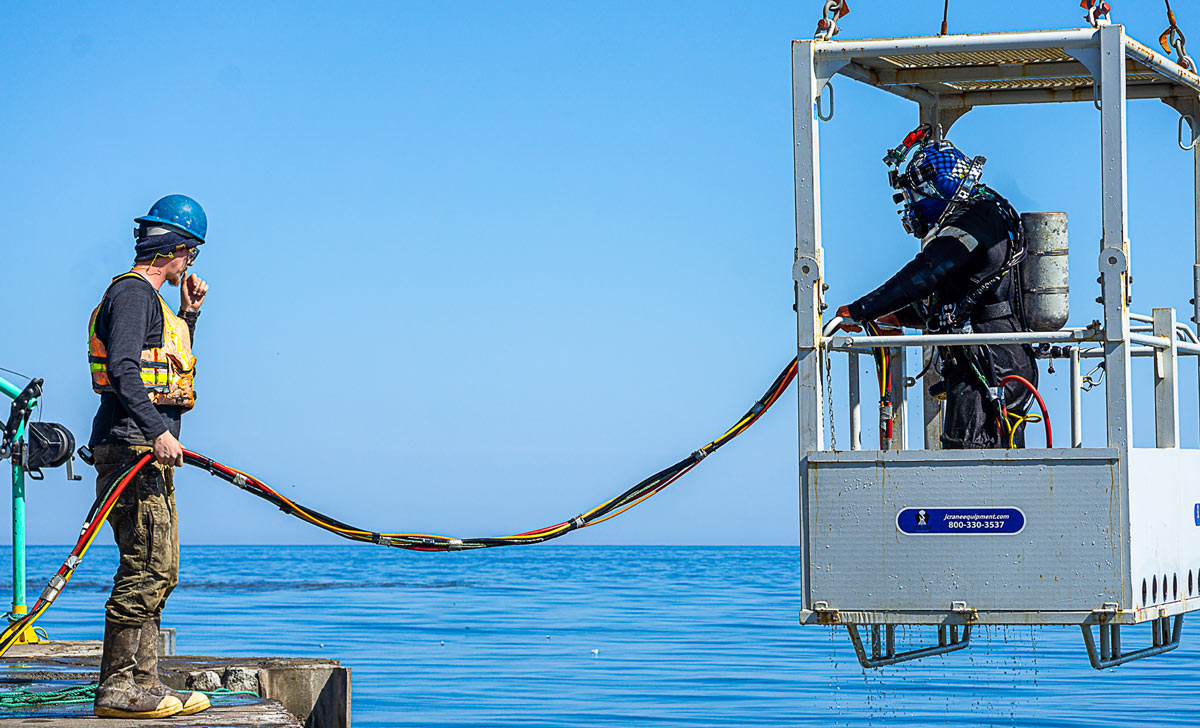
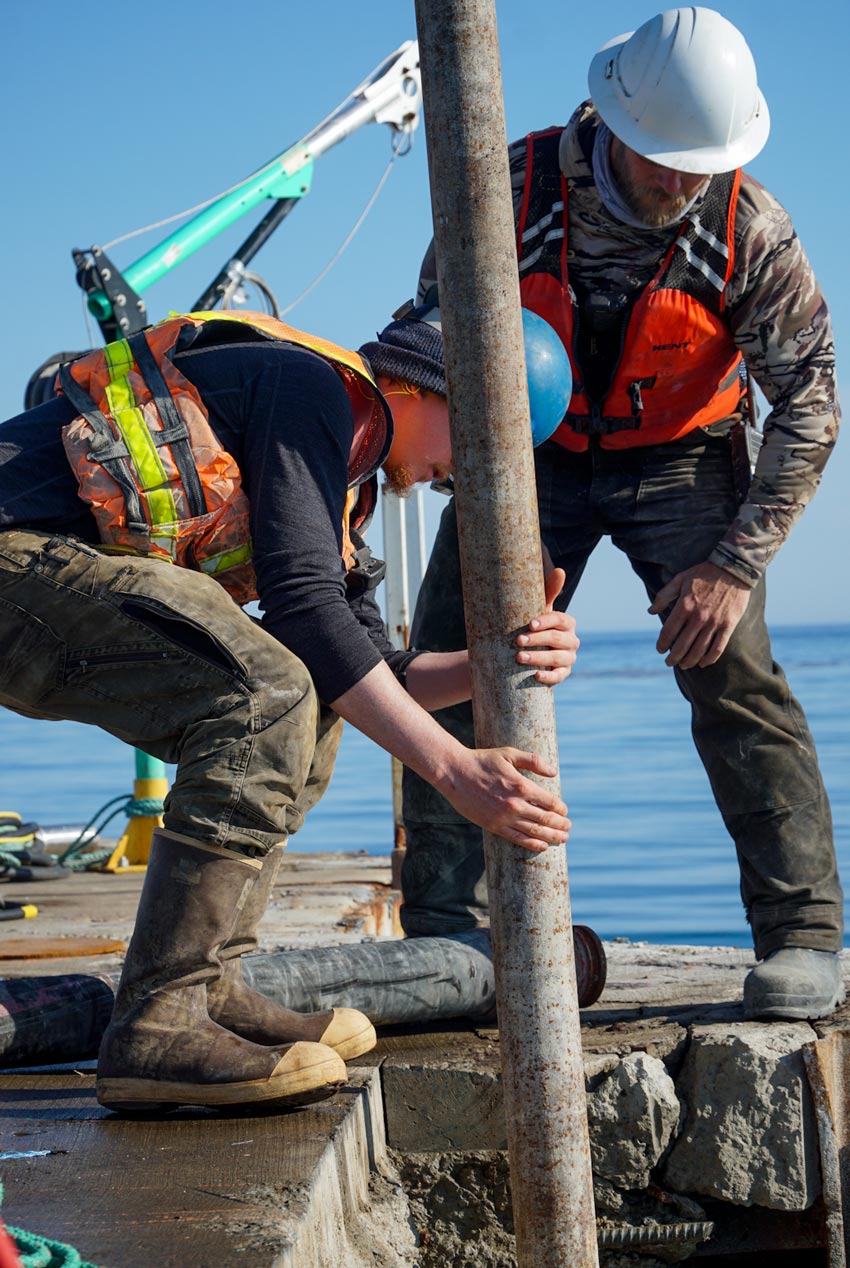
Photos courtesy of Karina Quintans
The storm that rocked Shemya Island in February 2020 compromised the structural integrity of the 75-foot by 320-foot World War II-era pier. The US government selected Brice Engineering and Appledore Marine Engineering, LLC to develop a plan for a fast-track, design-build, short-term repair.
“Without a breakwater or protective harbor, this exposed cellular steel structure has faced nearly eighty years of storm battery, only sustained by at least five repair and rehabilitation projects,” says Marcus Hobbs, a construction manager for Brice Environmental.
Brice served as the prime contractor and logistics lead while Appledore led the waterfront structural engineering. Global Diving and Salvage performed underwater repairs.
“We had an excellent team with complementary skills and knowledge that worked well together to complete the project on time and on budget and to client satisfaction despite multiple challenges along the way,” says Hobbs.
Those challenges included dealing with infamous and unpredictable weather (waves crashing against the pier have been recorded to reach as high as twenty feet); working at a remote location; working on a compressed schedule to complete the project in less than a year (the fuel pier is mission-critical to Eareckson Air Station); coordinating work around EAS operations; and modifying its plan when another storm caused further damage to the pier.
“With nothing available on this remote island, everything needed is sourced from around the country, staged in Seattle or Anchorage, and then barged 3,000 miles to Shemya Island months in advance, within a short window of time for safe travel across the ocean and the Bering Sea,” says Hobbs.
The temporary fix to the pier was completed during the summer of 2021, but the US Department of Defense recognized the need to fully repair the pier. In September of 2022, the US Army Corps of Engineers Alaska District awarded the project to a joint venture between Brice, a subsidiary of Calista Corporation, and Turnagain Marine Construction. Design work for the $176.7-million contract for the long-term pier repair project is underway. Construction is estimated to begin in 2023 or 2024.
During this project, a variety of companies will team up to complete the following goals: enlarge the 560-foot combi-wall system, encapsulate the existing pier, and include an entirely new deck and shoreline revetment system:
- Brice Environmental Services: Managing JV partner and project/construction manager, Shemya logistics and construction expertise
- Turnagain Marine Construction: Managing JV partner, specializes in marine structure installation
- Stantec Consulting: Subcontractor designer of record
- Appledore Marine Engineering, LLC: Subcontractor structural and waterfront engineering
- R & M Consultants: Subcontractor specialty geotechnical engineering
“There will be a substantial amount of materials needed to accomplish this project, to include steel pipe piling, precast concrete shoreline protection units, armor rock, a concrete batch plant, and materials to produce more than 15,000 cubic yards of concrete,” says Hobbs. “Altogether, a dozen barge trips with a 10,000-ton capacity will be needed to move necessary equipment and materials.”